Obsolescence management: Alstom’s proactive approach to keeping trains on track
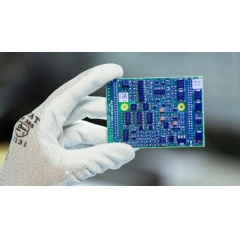
If your train was built to run for 30 years, but designed with parts that become obsolete in 10 years, what do you do when a part needs replacing? Stuart Broadbent, Alstom Obsolescence Management Director, explains how a dedicated team of engineers are continually searching for the best solutions for customers.
Stuart Broadbent, Obsolescence Management Director, is responsible for all aspects of obsolescence management in Alstom, where he has been working since 1980.
He has expertise across commercial, engineering, information systems, logistics, manufacturing, and project management in the rail engineering business.
Stuart is also Director of the International Institute of Obsolescence Management (IIOM) and Chair of the IIOM UK Chapter.
Why is obsolescence management critical for rail assets?SB: Rail assets – trains, signalling systems or infrastructure – have a life of 30 to 40 years. But, within the products that we supply, we use components that have a production life of perhaps only five years, particularly electronic components. It is not possible to replace individual components continuously in our designs, because that would require the revalidation of the train’s systems and subsystems. That’s why it’s really important to manage obsolescence because our customers expect our trains to last 35 years, even though a mid-life train may contain components that have not been produced for 10 or 20 years.
Electronic components in today’s trains are everywhere, for example, in door control units, the traction control, the train management system, and the brake system. So, when a train goes into service, the electronic equipment for the traction control and the train management system would have been designed five years earlier. Some of the electronic components will have been discontinued within five to ten years of the original design. We can no longer buy those chips from the original component manufacturer. This is what we have to manage.
How does Alstom manage obsolescence?We continuously monitor the availability of 60,000 electronic components; when a manufacturer is about to declare them obsolete, we decide whether to find a substitute for that component, redesign the part, or make a lifetime buy. Alstom often makes a lifetime buy, as redesigning and revalidating equipment is very expensive. Alstom has a significant amount of electronic components in stock to cover its production and service needs. We started doing obsolescence management because we had difficulty with electronic components, but also because we have long-term maintenance contracts. Customers are not interested in obsolescence; they want their trains ready for service as per the contract. Alstom is taking the risk of obsolescence in its service contracts, and we therefore must manage that risk. The advantage is that, because it matters to us, what we do for ourselves is also available to our customers.
When we identify obsolescence, the first thing we do is to notify our customers about it and propose solutions. When we offer solutions, we are looking to enhance the service customers get, either better reliability, better availability or more function. It is part of Alstom’s added value that we stay with our customer throughout the lifetime of the train. That is what our customers expect.
How does Alstom try to mitigate obsolescence issues?We make sure that we design in a way that reduces the risk of obsolescence, by choosing the right components, and designing them in a modular way, so that we can replace a component or sub-assembly of a piece of equipment without having to replace the whole unit. For example, wireless communications have changed from GSM, to 2G, 3G, 4G, and now 5G. 3G is now becoming obsolete. We don’t want to have to completely redesign a train because we can’t make a 3G connection anymore, so instead, modular design means that we can replace a 3G radio with a 4G or a 5G radio. We manage it at the system level and not just at the component level.
We are good at identifying what is going to become obsolete in the life of a train and we have a strategic approach to managing obsolescence. For high-risk parts, we think about how to manage obsolescence from the beginning and what will we do in 20 or 30 years to support this product. For medium-risk components, we monitor the availability of the part and then, when necessary, we will notify the customer and either make a lifetime buy or propose a replacement product. For low-risk parts we are reactive, and deal with the obsolescence problem when and if it occurs.
How big is Alstom’s obsolescence management network?Obsolescence management is a relatively new discipline and Alstom is working to develop it. We are members of the International Institute of Obsolescence Management, and we have access to their training programmes and their validation scheme for the competence level of individuals. Within Alstom, we have the World Class Engineering programme, where we identify and develop three levels of expert: expert; senior expert; and master expert. We have identified 150 people within Alstom who spend a significant amount of time in their job on obsolescence management, of whom 33 are experts, and we have a network which meets three times a year. In addition, it is important to train people in this new discipline. Since 2018, we have trained 3,000 people in Alstom in obsolescence management.
For me, one of the successes has been building and diversifying the community. We have people coming in at the beginning of their careers and learning the discipline of obsolescence management instead of engineers transferring in towards the end of their careers. It is changing the age profile, with people from various countries and a significant number of women engineers. We are also working with a university in Paris and providing two tutors for their Master’s course in obsolescence management, which starts in 2025.
How does Alstom’s obsolescence expertise benefit customers?We ensure that customer assets can last for the planned design life and perhaps longer. With so much advanced technology in rolling stock, operators now rely on Alstom because of our expertise in sustaining their assets. We help them to secure the asset life, and in the long term, to secure reliability and availability, as well as ensuring our trains do not go out of service early because of obsolescence. We work with our customers on developing their skills and helping their understanding of the issue. We are often competing with manufacturers who don’t think about obsolescence risk, so it is important that our customers not only understand the risk to their fleets of obsolescence but also consider obsolescence management in their tenders.
( Press Release Image: https://photos.webwire.com/prmedia/6/324027/324027-1.jpg )
WebWireID324027
This news content was configured by WebWire editorial staff. Linking is permitted.
News Release Distribution and Press Release Distribution Services Provided by WebWire.