For clean ammonia, MIT engineers propose going underground
Using the Earth itself as a chemical reactor could reduce the need for fossil-fuel-powered chemical plants.
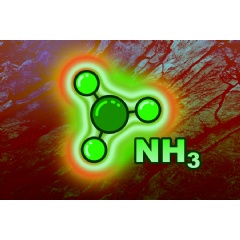
Ammonia is the most widely produced chemical in the world today, used primarily as a source for nitrogen fertilizer. Its production is also a major source of greenhouse gas emissions — the highest in the whole chemical industry.
Now, a team of researchers at MIT has developed an innovative way of making ammonia without the usual fossil-fuel-powered chemical plants that require high heat and pressure. Instead, they have found a way to use the Earth itself as a geochemical reactor, producing ammonia underground. The processes uses Earth’s naturally occurring heat and pressure, provided free of charge and free of emissions, as well as the reactivity of minerals already present in the ground.
The trick the team devised is to inject water underground, into an area of iron-rich subsurface rock. The water carries with it a source of nitrogen and particles of a metal catalyst, allowing the water to react with the iron to generate clean hydrogen, which in turn reacts with the nitrogen to make ammonia. A second well is then used to pump that ammonia up to the surface.
The process, which has been demonstrated in the lab but not yet in a natural setting, is described today in the journal Joule. The paper’s co-authors are MIT professors of materials science and engineering Iwnetim Abate and Ju Li, graduate student Yifan Gao, and five others at MIT.
“When I first produced ammonia from rock in the lab, I was so excited,” Gao recalls. “I realized this represented an entirely new and never-reported approach to ammonia synthesis.’”
The standard method for making ammonia is called the Haber-Bosch process, which was developed in Germany in the early 20th century to replace natural sources of nitrogen fertilizer such as mined deposits of bat guano, which were becoming depleted. But the Haber-Bosch process is very energy intensive: It requires temperatures of 400 degrees Celsius and pressures of 200 atmospheres, and this means it needs huge installations in order to be efficient. Some areas of the world, such as sub-Saharan Africa and Southeast Asia, have few or no such plants in operation. As a result, the shortage or extremely high cost of fertilizer in these regions has limited their agricultural production.
The Haber-Bosch process “is good. It works,” Abate says. “Without it, we wouldn’t have been able to feed 2 out of the total 8 billion people in the world right now, he says, referring to the portion of the world’s population whose food is grown with ammonia-based fertilizers. But because of the emissions and energy demands, a better process is needed, he says.
Burning fuel to generate heat is responsible for about 20 percent of the greenhouse gases emitted from plants using the Haber-Bosch process. Making hydrogen accounts for the remaining 80 percent. But ammonia, the molecule NH3, is made up only of nitrogen and hydrogen. There’s no carbon in the formula, so where do the carbon emissions come from? The standard way of producing the needed hydrogen is by processing methane gas with steam, breaking down the gas into pure hydrogen, which gets used, and carbon dioxide gas that gets released into the air.
Other processes exist for making low- or no-emissions hydrogen, such as by using solar or wind-generated electricity to split water into oxygen and hydrogen, but that process can be expensive. That’s why Abate and his team worked on developing a system to produce what they call geological hydrogen. Some places in the world, including some in Africa, have been found to naturally generate hydrogen underground through chemical reactions between water and iron-rich rocks. These pockets of naturally occurring hydrogen can be mined, just like natural methane reservoirs, but the extent and locations of such deposits are still relatively unexplored.
Abate realized this process could be created or enhanced by pumping water, laced with copper and nickel catalyst particles to speed up the process, into the ground in places where such iron-rich rocks were already present. “We can use the Earth as a factory to produce clean flows of hydrogen,” he says.
He recalls thinking about the problem of the emissions from hydrogen production for ammonia: “The ‘aha!’ moment for me was thinking, how about we link this process of geological hydrogen production with the process of making Haber-Bosch ammonia?”
That would solve the biggest problem of the underground hydrogen production process, which is how to capture and store the gas once it’s produced. Hydrogen is a very tiny molecule — the smallest of them all — and hard to contain. But by implementing the entire Haber-Bosch process underground, the only material that would need to be sent to the surface would be the ammonia itself, which is easy to capture, store, and transport.
The only extra ingredient needed to complete the process was the addition of a source of nitrogen, such as nitrate or nitrogen gas, into the water-catalyst mixture being injected into the ground. Then, as the hydrogen gets released from water molecules after interacting with the iron-rich rocks, it can immediately bond with the nitrogen atoms also carried in the water, with the deep underground environment providing the high temperatures and pressures required by the Haber-Bosch process. A second well near the injection well then pumps the ammonia out and into tanks on the surface.
“We call this geological ammonia,” Abate says, “because we are using subsurface temperature, pressure, chemistry, and geologically existing rocks to produce ammonia directly.”
Whereas transporting hydrogen requires expensive equipment to cool and liquefy it, and virtually no pipelines exist for its transport (except near oil refinery sites), transporting ammonia is easier and cheaper. It’s about one-sixth the cost of transporting hydrogen, and there are already more than 5,000 miles of ammonia pipelines and 10,000 terminals in place in the U.S. alone. What’s more, Abate explains, ammonia, unlike hydrogen, already has a substantial commercial market in place, with production volume projected to grow by two to three times by 2050, as it is used not only for fertilizer but also as feedstock for a wide variety of chemical processes.
For example, ammonia can be burned directly in gas turbines, engines, and industrial furnaces, providing a carbon-free alternative to fossil fuels. It is being explored for maritime shipping and aviation as an alternative fuel, and as a possible space propellant.
Another upside to geological ammonia is that untreated wastewater, including agricultural runoff, which tends to be rich in nitrogen already, could serve as the water source and be treated in the process. “We can tackle the problem of treating wastewater, while also making something of value out of this waste,” Abate says.
Gao adds that this process “involves no direct carbon emissions, presenting a potential pathway to reduce global CO2 emissions by up to 1 percent.” To arrive at this point, he says, the team “overcame numerous challenges and learned from many failed attempts. For example, we tested a wide range of conditions and catalysts before identifying the most effective one.”
The project was seed-funded under a flagship project of MIT’s Climate Grand Challenges program, the Center for the Electrification and Decarbonization of Industry. Professor Yet-Ming Chiang, co-director of the center, says “I don’t think there’s been any previous example of deliberately using the Earth as a chemical reactor. That’s one of the key novel points of this approach.” Chiang emphasizes that even though it is a geological process, it happens very fast, not on geological timescales. “The reaction is fundamentally over in a matter of hours,” he says. “The reaction is so fast that this answers one of the key questions: Do you have to wait for geological times? And the answer is absolutely no.”
Professor Elsa Olivetti, a mission director of the newly established Climate Project at MIT, says, “The creative thinking by this team is invaluable to MIT’s ability to have impact at scale. Coupling these exciting results with, for example, advanced understanding of the geology surrounding hydrogen accumulations represent the whole-of-Institute efforts the Climate Project aims to support.”
“This is a significant breakthrough for the future of sustainable development,” says Geoffrey Ellis, a geologist at the U.S. Geological Survey, who was not associated with this work. He adds, “While there is clearly more work that needs to be done to validate this at the pilot stage and to get this to the commercial scale, the concept that has been demonstrated is truly transformative. The approach of engineering a system to optimize the natural process of nitrate reduction by Fe2+ is ingenious and will likely lead to further innovations along these lines.”
The initial work on the process has been done in the laboratory, so the next step will be to prove the process using a real underground site. “We think that kind of experiment can be done within the next one to two years,” Abate says. This could open doors to using a similar approach for other chemical production processes, he adds.
The team has applied for a patent and aims to work towards bringing the process to market.
“Moving forward,” Gao says, “our focus will be on optimizing the process conditions and scaling up tests, with the goal of enabling practical applications for geological ammonia in the near future.”
The research team also included Ming Lei, Bachu Sravan Kumar, Hugh Smith, Seok Hee Han, and Lokesh Sangabattula, all at MIT. Additional funding was provided by the National Science Foundation and was carried out, in part, through the use of MIT.nano facilities.
( Press Release Image: https://photos.webwire.com/prmedia/6/332930/332930-1.jpg )
WebWireID332930
This news content was configured by WebWire editorial staff. Linking is permitted.
News Release Distribution and Press Release Distribution Services Provided by WebWire.